As a Safety professional, I strongly emphasize that safety data analysis is crucial for reducing workplace incidents. By analyzing safety data, organizations can identify areas for improvement and develop targeted training programs using tools like electronic safety management systems.
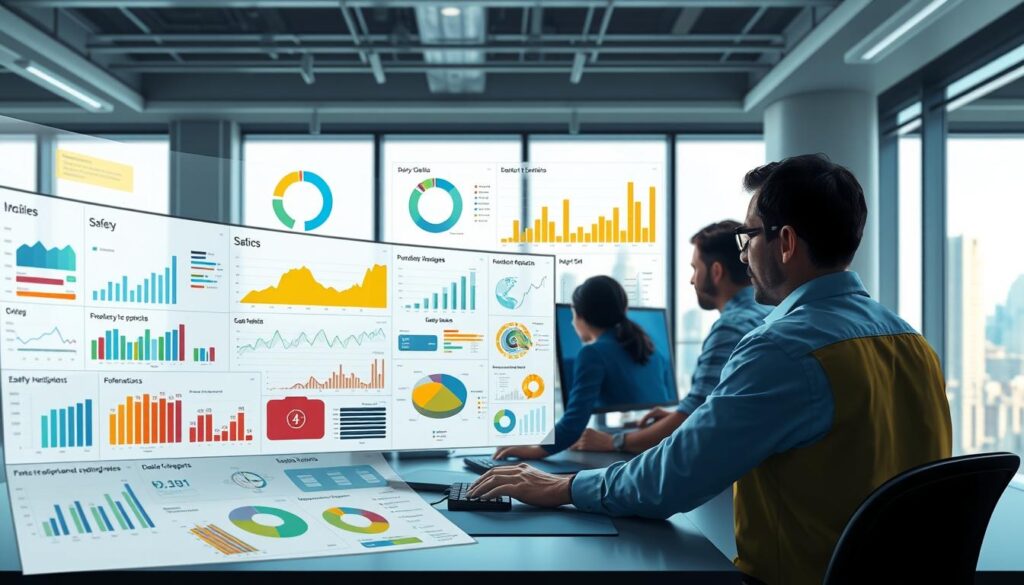
How to Train Your Crew to Use Safety Tools the Right Way?
Effective safety practices are essential for preventing workplace incidents. I have seen firsthand the impact of proper safety tool usage on incident reduction.
Proper training is key to ensuring that crews use safety tools correctly. By focusing on safety data analysis and proper tool usage, organizations can significantly reduce incidents.
The Critical Role of Proper Safety Tool Usage in Preventing Workplace Incidents
The correct utilization of safety tools is crucial in minimizing workplace accidents. Proper safety tool usage not only ensures a safe working environment but also significantly reduces the risk of incidents that could lead to injuries or fatalities.
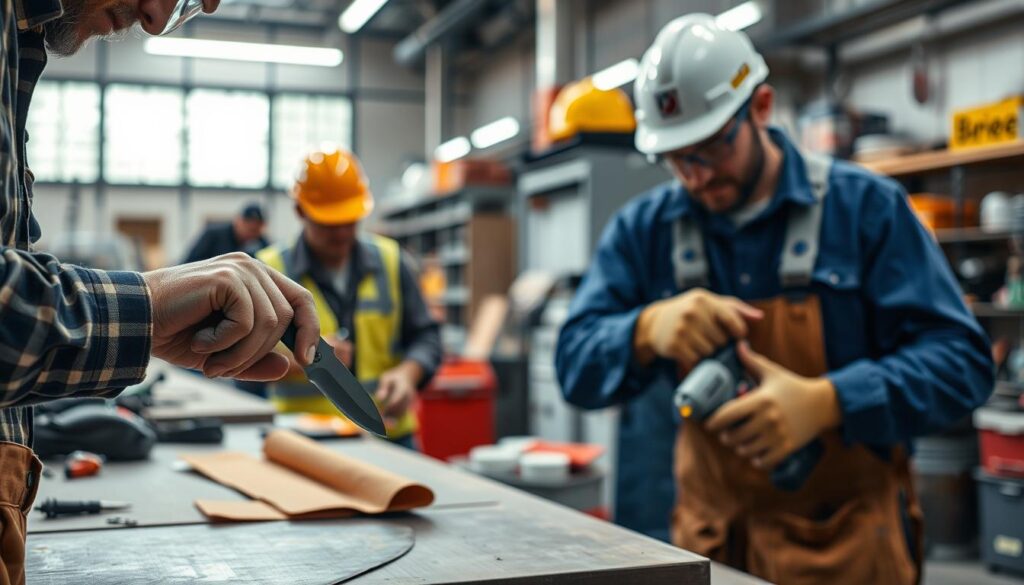
Current Statistics on Safety Tool-Related Incidents in the Canada
Recent statistics indicate that a significant number of workplace incidents in Canada are attributed to the improper use of safety tools. According to the Bureau of Labor Statistics, thousands of workers are injured annually due to improper safety tool usage. These incidents not only affect the workers but also have a broader impact on the overall productivity and safety culture of the organization.
The Cost of Improper Safety Tool Usage
The cost associated with improper safety tool usage is substantial, encompassing both direct and indirect costs. Direct costs include medical expenses and workers’ compensation claims, while indirect costs involve lost productivity, training replacement workers, and potential legal liabilities. Ensuring proper safety tool usage can significantly mitigate these costs.
How Effective Training Reduces Incident Rates
Effective crew safety training and safety tool training are critical in reducing incident rates, especially when combined with online safety training methods tailored to Canadian workplaces. By providing workers with comprehensive training on the correct usage of safety tools, organizations can significantly minimize the risk of workplace incidents. This not only enhances the safety culture but also contributes to a more efficient and productive work environment.
Analyzing Safety Data to Identify Training Needs
Safety data analysis plays a vital role in pinpointing areas that require additional training, which can then be addressed through customized health and safety programs. By examining safety data, organizations can gain valuable insights into their safety performance and identify areas for improvement.
Key Safety Metrics to Track and Analyze
To effectively analyze safety data, it’s essential to track and analyze key safety metrics. These include:
- Incident Frequency Rates: The number of incidents occurring within a specific timeframe.
- Incident Severity Rates: The severity of incidents, including the impact on employees and operations.
- Near-Miss Incidents: Events that could have resulted in incidents but were narrowly avoided.
By monitoring these metrics, organizations can identify trends and patterns in their safety data.
Identifying Patterns in Safety Incidents
Analyzing safety data helps organizations identify patterns in safety incidents. This involves examining the data to determine common causes, locations, and times when incidents occur. By recognizing these patterns, organizations can target their training efforts more effectively—just like in data-driven safety success stories where near-miss reports were used to refine training.
Using Data to Develop Targeted Training Programs
The insights gained from safety data analysis can be used to develop targeted training programs. These programs address the specific needs identified through the analysis, ensuring that training is relevant and effective. For instance, if the data indicates a high frequency of incidents related to a particular task, additional training can be provided to employees performing that task.
By leveraging safety data analysis, organizations can create a more informed and proactive approach to safety training, ultimately reducing the risk of incidents and improving overall safety performance.
How to Train Your Crew to Use Safety Tools the Right Way
Effective safety tool training is crucial for preventing workplace incidents. In this section, we will discuss the importance of establishing clear safety tool protocols, hands-on training techniques, and verification of competency and certification.
Establishing Clear Safety Tool Protocols
Clear safety tool protocols are essential for ensuring that your crew uses safety tools correctly. To achieve this, it is vital to establish protocols that are easy to follow and understand.
Hands-On Training Techniques That Work
Hands-on training is an effective way to teach your crew how to use safety tools correctly. There are several techniques that have proven to be successful in this regard.
Demonstration and Practice Methods
Demonstration and practice are two essential components of hands-on training. By demonstrating the correct usage of safety tools, you can help your crew understand the proper procedures and techniques involved.
Scenario-Based Training Approaches
Scenario-based training is another effective approach to hands-on training. This involves presenting your crew with realistic scenarios that simulate real-world situations, allowing them to practice their skills in a controlled environment.
Verification of Competency and Certification
Verifying the competency and certification of your crew is crucial for ensuring that they are proficient in using safety tools. This involves assessing their knowledge and skills to ensure that they meet the required standards and regulations.
Implementing Ongoing Safety Tool Training Programs
Effective safety tool training programs are essential for reducing workplace incidents and enhancing crew safety compliance. To achieve this, organizations must adopt a multifaceted approach that includes regular training, updated procedures, and a culture of compliance.
Regular Refresher Training Schedules
Regular refresher training is crucial for ensuring that crews remain competent in using safety tools. I recommend scheduling refresher training at least twice a year, or more frequently if required by regulatory standards or company policy. This not only reinforces proper safety tool usage but also addresses any complacency that may have developed since the initial training.
For instance, a construction company might implement a bi-annual refresher training program that includes hands-on exercises and scenario-based training to keep workers proficient in using safety harnesses and fall protection equipment.
Addressing New Safety Tools and Updated Procedures
As new safety tools are introduced or procedures are updated, it’s essential to incorporate these changes into the training program. This ensures that crews are always trained on the latest safety tool procedures and guidelines. I suggest conducting a thorough review of existing training materials whenever new equipment is introduced or procedures are modified.
For example, if a company adopts a new type of personal protective equipment (PPE), similar to what’s covered in our fall protection guide, the training program should be updated to include information on the proper use, maintenance, and inspection of this equipment.
Creating a Culture of Safety Tool Compliance
Creating a culture of safety tool compliance within an organization requires a commitment from all levels of the organization. I believe that leadership plays a critical role in promoting a safety-first culture by setting clear expectations and leading by example. Regular audits and feedback mechanisms can also help ensure that safety protocols are being followed.
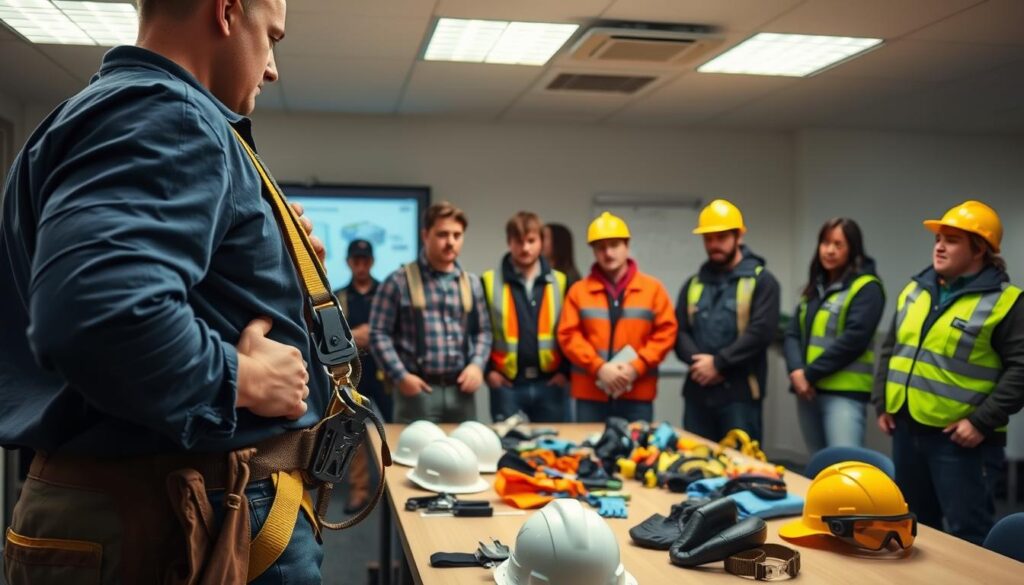
By implementing ongoing safety tool training programs, organizations can significantly reduce the risk of workplace incidents. This involves not only providing regular refresher training but also staying up-to-date with new safety tools and procedures, and fostering a culture that values safety above all else.
Conclusion:
To ensure the effectiveness of a safety tool training program, it’s crucial to measure its impact through continuous safety data analysis. By regularly assessing incident rates and training outcomes, organizations can identify areas for improvement and make data-driven decisions to enhance their safety practices.
I have discussed the importance of proper safety tool usage, analyzing safety data to identify training needs, and implementing ongoing training programs. By tracking key safety metrics and verifying competency, organizations can refine their training programs to achieve better results.
Effective measurement of a safety tool training program involves not just initial training but also regular refresher training and updates on new safety tools and procedures. This approach helps create a culture of safety tool compliance, ultimately reducing workplace incidents and aligning with broader workplace safety certification goals.By focusing on safety data analysis and continuous improvement, organizations can maximize the impact of their safety tool training programs and foster a safer work environment.