Working in the construction industry, I stress the need for regular fall protection equipment inspections. These checks are not just routine; they are crucial for worker safety and regulation compliance. Ignoring them can lead to accidents, fines, and legal issues.
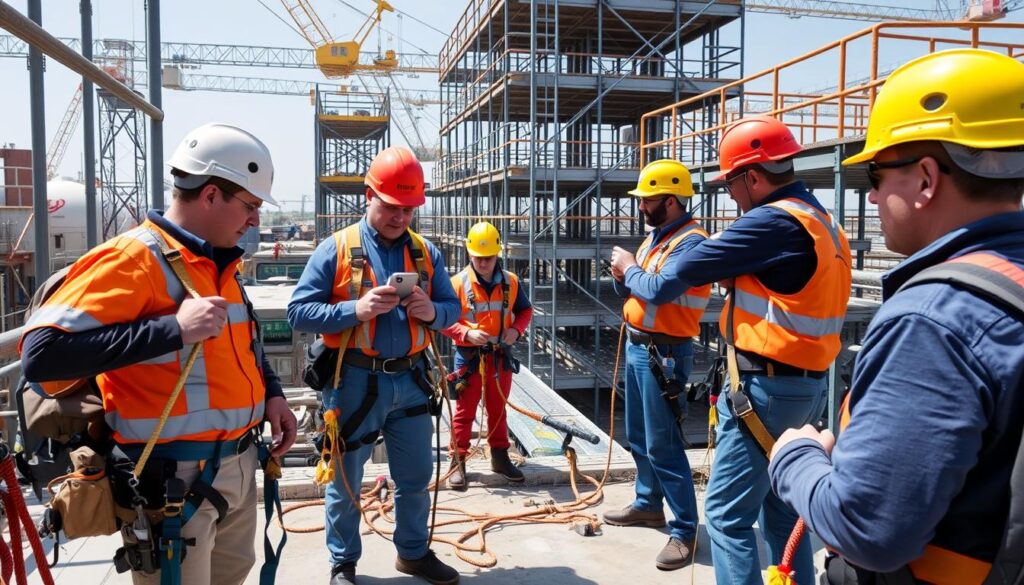
Fall protection systems are vital for construction site safety. Regular inspections help maintain their effectiveness. By checking equipment, workers can spot problems early, prevent accidents, and protect themselves and business.
This article will cover the basics of fall protection systems and regulations. It will also guide you through conducting detailed inspections. Understanding and following these steps can make our work environment safer, ensuring projects are completed safely and efficiently.
The Fundamentals of Fall Protection Systems
Maintaining workplace safety is paramount, and fall protection systems play a crucial role in safeguarding workers who operate at heights. Understanding the fundamentals of these systems is essential for ensuring their proper selection, installation, and use.
Types of Fall Protection Equipment
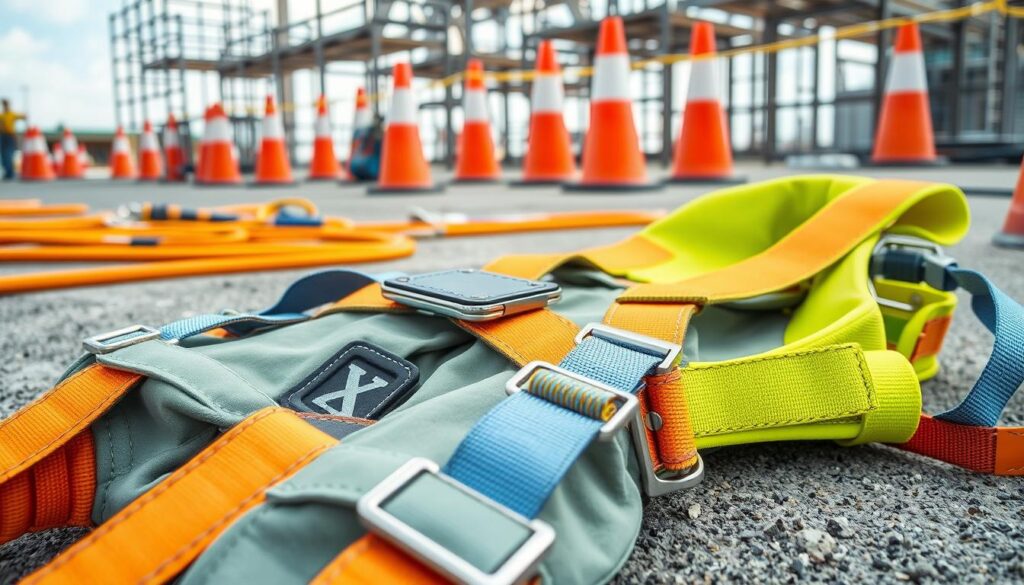
Fall protection equipment encompasses a wide range of devices designed to mitigate the risks associated with working at elevated levels. Common types of equipment include full-body harnesses, lanyards, shock-absorbing systems, self-retracting lifelines, and anchor points. Each type of equipment serves a specific purpose and must be chosen based on the unique requirements of the work environment.
Key Components of Fall Arrest Systems
A fall arrest system is a comprehensive solution that combines multiple components to arrest a worker’s fall and minimize the impact. These systems typically include a full-body harness, a connecting device (such as a lanyard or self-retracting lifeline), and a reliable anchor point. Proper selection and integration of these components are essential for ensuring the system’s effectiveness and worker safety.
Industry Standards and Applications
The use of fall protection equipment is governed by industry standards and regulations. These standards outline the specific requirements for the selection, installation, and use of fall protection systems in various work environments, including construction, telecommunications, and general industry. Adherence to these standards is crucial for maintaining compliance and protecting workers from the risks of falls.
Fall Protection Equipment | Key Features | Typical Applications |
Full-Body Harness | Distributes fall forces across the body, provides attachment points for connecting devices | Construction, telecommunications, general industry |
Shock-Absorbing Lanyard | Reduces the impact forces on the worker during a fall, limits the maximum deceleration | Construction, telecommunications, general industry |
Self-Retracting Lifeline | Automatically locks and limits the worker’s fall distance, provides a steady connection to the anchor point | Construction, general industry, maintenance |
By understanding the fundamentals of fall protection systems, including the various types of equipment and their key components, as well as the industry standards and applications, employers and workers can ensure the proper selection, installation, and use of these critical safety systems.
Also Read: 5 Types of Fall Protection Systems and When to Use Them
Fall Protection Inspections: A Safety Must For Workers
Keeping a workplace safe is a top priority for any organization. Regular checks on fall protection equipment are crucial. Responsible workers know how vital it is to do thorough pre-use checks on their personal protective equipment (PPE). This ensures it’s in top shape and can protect them from job site hazards.
Pre-Use Inspection Protocols
Before starting any work at height, workers must always inspect their fall protection gear carefully. They should look for signs of wear or damage, like frayed webbing or broken hardware. They should also test its full range of motion to make sure it won’t restrict any movements.
Documentation and Record Keeping
- Detailed records of all fall protection equipment inspections should be kept. This includes its use history, maintenance, and any repairs or replacements.
- This record helps track the equipment’s condition. It’s also useful for the safety team and regulatory bodies if needed.
Common Wear and Tear Signs
Even the best-maintained fall protection gear can show wear and tear over time. Watch for fraying, cracks, deformation, and corrosion. These signs can weaken the equipment and put workers at risk.
If deficiencies are found, remove it from service and report it to your supervisor for evaluation and replacement.
Inspection Item | Acceptable Condition | Unacceptable Condition |
Webbing | Intact, free of fraying or cuts | Frayed, cut, or otherwise damaged |
Hardware | Functioning properly, with no cracks or deformation | Cracked, bent, or malfunctioning |
Stitching | Secure, no loose or missing stitches | Loose, missing, or damaged stitching |
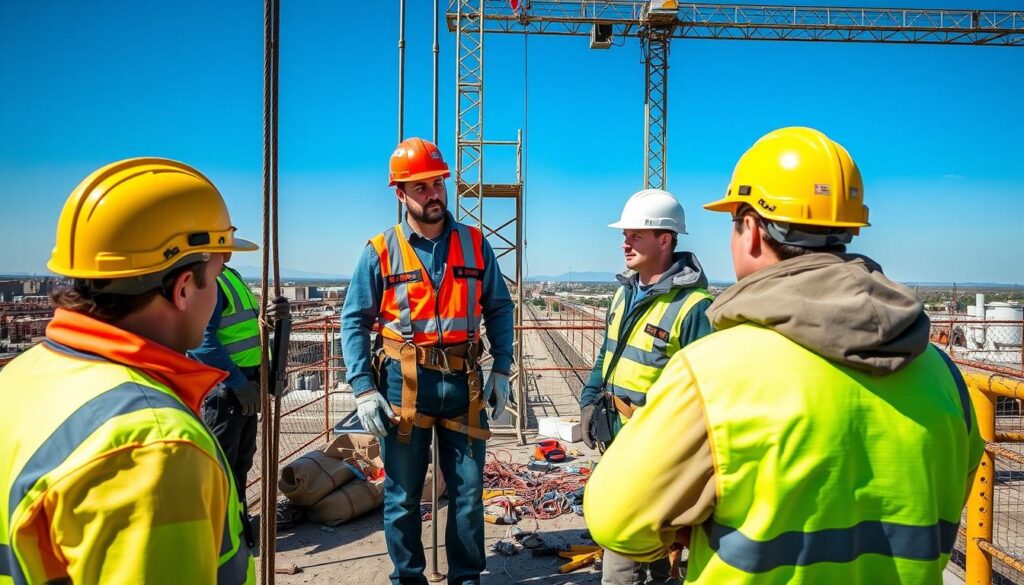
By following these inspection protocols and watching for common wear and tear, fall protection equipment is kept in top condition. This ensures workers have the necessary safety measures and can work at height confidently. Regular inspections are a small but crucial step toward a safe and productive job site.
Essential Components of Harness Inspection
Maintaining and regularly inspecting personal protective equipment (PPE) like fall protection harnesses is crucial for worker safety. Harness inspection focuses on several key components to ensure the equipment’s reliability and effectiveness.
Inspecting the webbing, the load-bearing part of the harness is a critical step. Look for any damage, such as cuts, fraying, or excessive wear. Also, check that all stitching is intact and secure, vital for the harness’s strength and integrity.
- Inspect all buckles, D-rings, and hardware for deformation, corrosion, or malfunction.
- Verify the harness’s label is legible and includes the necessary information, like the manufacturer’s instructions and a unique identification number.
- Search for signs of chemical exposure or damage, which could weaken the harness’s structure.
The frequency of harness inspections depends on the manufacturer’s guidelines and usage patterns. It’s recommended to inspect before each use and have a detailed annual inspection by a professional. Following these guidelines ensures harnesses are in top condition, providing necessary protection during critical situations.
Inspection Criteria | Acceptable Condition | Unacceptable Condition |
Webbing | No cuts, fraying, or excessive wear | Cuts, fraying, or excessive wear |
Stitching | Intact and secure | Damaged or loose |
Buckles and Hardware | No deformation or corrosion | Deformed or corroded |
Labels | Legible and complete | Illegible or missing |
Chemical Exposure | No signs of damage | Signs of chemical damage |
By following these detailed harness inspection protocols, workers can maintain their personal protective equipment (PPE) in peak condition. This ensures they are protected in the event of a fall.
Anchor Point Verification and Testing Procedures
In the realm of fall protection, verifying and testing anchor points is paramount. These points are the backbone of fall arrest systems, crucial for safeguarding workers from falls. It’s imperative to inspect and validate their integrity meticulously. This ensures the safety and reliability of these systems.

Load Testing Requirements
Load testing is a fundamental aspect of anchor point verification. Industry standards dictate that anchor points must withstand a minimum load of 5,000 pounds. This is either twice the maximum expected load or greater, whichever applies. I ensure that only a qualified individual conducts these tests with calibrated equipment, adhering strictly to the manufacturer’s guidelines.
Such rigorous testing uncovers any potential weaknesses or defects that could compromise the anchor point’s safety.
Installation Verification Steps
Inspection of anchor point installation is another critical step. Verify the anchor’s proper placement, alignment, and secure attachment. The structural integrity of the mounting surface is also examined, ensuring it can support the necessary loads without compromising stability. This thorough verification confirms the anchor point’s ability to safely arrest a fall.
Maintenance Schedules
Maintaining anchor points’ reliability is a key responsibility. There should be a detailed maintenance schedule. This includes regular visual inspections, functional testing, and preventive maintenance. This proactive approach helps workers identify and address wear, corrosion, or damage early on. By following these maintenance protocols, workers ensure the anchor points remain reliable and consistent in their protection.
Conclusion
Regular fall protection inspections are not just a regulatory requirement—they are a cornerstone of workplace safety. By ensuring that all fall protection systems are in optimal condition, you not only protect your employees from potential hazards but also foster a culture of safety and compliance.
These inspections help identify issues before they become dangerous, reduce liability risks, and ultimately save lives.
Also Read: Common Fall Protection Mistakes and How to Avoid Them
Investing time and resources in thorough, regular inspections demonstrates a commitment to safety that goes beyond mere compliance. It safeguards your workforce, improves morale, and contributes to a more productive environment. Remember: when it comes to fall protection, prevention is always better than response. Make inspections a priority, and you’ll build a safer, stronger workplace for everyone.