As a workplace safety professional, I’ve seen firsthand the importance of fall protection. It’s crucial for keeping employees safe. Yet, many organizations make the same mistakes over and over.
In this article, we’ll discuss the common fall protection mistakes and offer practical ways to prevent them. This will improve workplace safety and ensure compliance.

.
Falls from heights are a major cause of serious injuries and deaths at work. The legislative reports that falls are responsible for nearly 40% of construction-related fatalities. Despite the need for fall protection systems, they are often ignored or used incorrectly. This puts workers at risk. By tackling these common issues, we can make workplaces safer and protect our employees.
In the following sections, I’ll cover fall protection in detail. This includes the necessary equipment, common fall protection mistakes to avoid, and compliance requirements. Understanding these elements will help you protect your workforce and meet legislation standards.
Understanding Basic Fall Protection Equipment Requirements
Worker safety on construction sites is paramount, and proper fall protection equipment is key. We’ll delve into the critical parts of a personal fall arrest system, the vital features of a safety harness, and the need for regular inspections.
Types of Personal Fall Arrest Systems
Personal fall arrest systems aim to catch workers in case of a fall, preventing severe injury or death. These systems consist of a full-body harness, a connecting device like a lanyard, and an anchor point that can hold the worker’s weight. It’s vital to know the various fall arrest systems and their correct uses for site safety.
Essential Components of a Safety Harness
The safety harness is at the core of a personal fall arrest system, securing the worker in a fall. A good harness has adjustable straps, strong attachment points, and padding for comfort. It’s crucial to check the harness regularly for wear or damage to ensure safety.
Proper Equipment Inspection Protocols
Regularly inspecting fall protection gear is a vital safety measure. Workers should examine their harnesses, lanyards, and other parts before each use for wear, damage, or deterioration.
Any faulty equipment must be taken out of service and replaced. Following manufacturer guidelines and keeping detailed inspection records is essential to avoid fall protection mistakes.

“Proper use and maintenance of fall protection equipment is essential for safeguarding workers at height. Investing in quality gear and following rigorous inspection protocols can mean the difference between a safe workday and a tragic incident.”
Top Fall Protection Mistakes and Prevention Tips
Fall protection is a cornerstone of workplace safety. Yet, many organizations overlook common mistakes that undermine their fall protection systems. We will delve into these errors and offer practical advice to prevent them.
One frequent issue is the misuse of guardrails. These barriers are meant to prevent falls. However, if not installed or maintained properly, they fail to serve their purpose. It’s crucial to regularly inspect and repair any damaged or missing guardrails to ensure a safe work environment.
Another common error is the improper use of safety nets. These nets are vital to avoid fall protection mistakes, but only if used correctly and at the right height. Neglecting to follow manufacturer guidelines or failing to inspect nets for damage can render them ineffective.
Lastly, ladder safety is often neglected, leading to accidents that could be prevented. Ensuring ladders are set up correctly, including securing the base and extending at least 3 feet above the landing, is essential. Workers must also be trained on ladder safety, including maintaining three points of contact and avoiding overreaching.
- Regularly inspect and maintain guardrails to ensure they are in proper working condition.
- Follow manufacturer guidelines when installing and using safety nets, and inspect them regularly for wear and tear.
- Provide comprehensive training on ladder safety, including proper setup and usage protocols.
By addressing these common fall protection mistakes and implementing the suggested prevention tips, organizations can significantly enhance their workplace safety. This will protect their employees from the risks of falls.
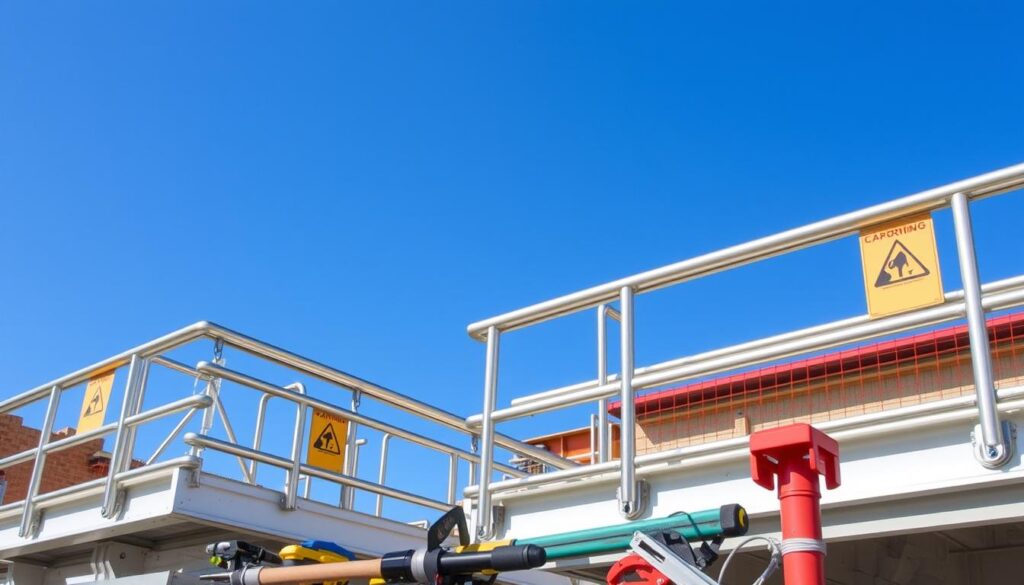
work environment.
“Fall protection is not just a requirement, it’s a necessity for maintaining a safe and productive work environment.”
Critical Anchor Point and Connection Issues
Ensuring the integrity and reliability of anchor points is vital for fall protection. These points are the foundation for personal fall arrest systems. Their load-bearing capacity is crucial in preventing catastrophic failures.
Proper selection and connection of hardware components are also essential for a fall protection system’s effectiveness.
Load Rating Requirements for Anchor Points
Anchor points must withstand the forces generated during a fall arrest. The minimum load-bearing capacity for an anchor point is typically 5,000 pounds per attached worker. Failure to meet these load rating requirements can lead to anchor point failure.
This can have devastating consequences for the worker. Regularly inspecting anchor points and ensuring they are suitable for the intended use is a critical safety measure.
Common Connection Hardware Failures
Improper or worn connection hardware can compromise a fall protection system’s integrity. Carabiners, lanyards, and other components are subject to wear and tear. Any signs of damage or deterioration must be addressed promptly. Replacing faulty hardware is essential to maintain the system’s reliability and protect workers from the risk of dropped objects.
Proper Tie-Off Techniques
Correctly tying off to an anchor point is crucial for ensuring the effectiveness against fall protection mistakes. Workers must be trained on proper tie-off methods.
This includes ensuring the tie-off point is at or above the user’s D-ring, minimizing free fall distance, and avoiding tie-offs that could result in contact with lower levels or objects. Adherence to these techniques can significantly reduce the risk of injury in the event of a fall.
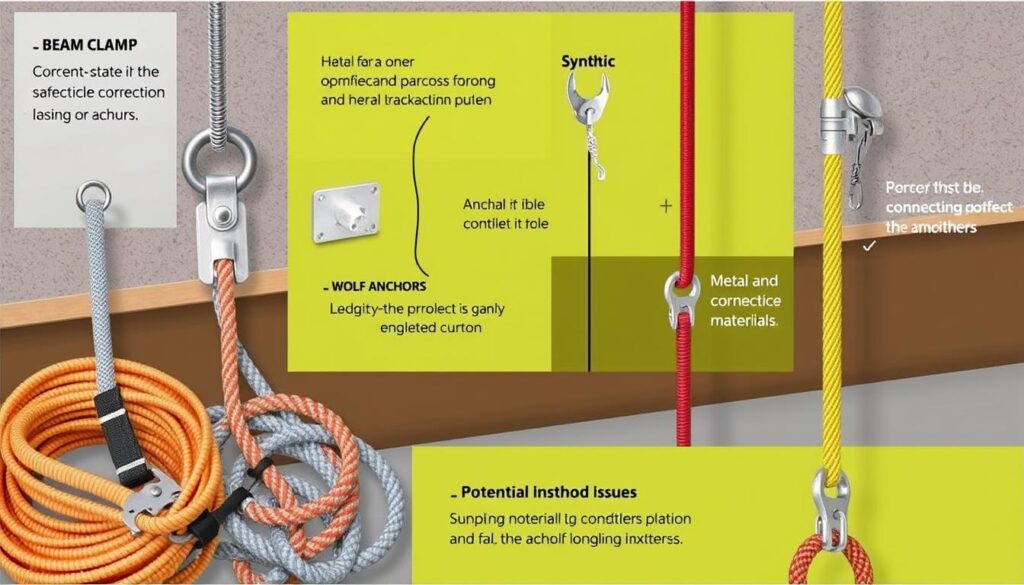
By addressing the critical issues surrounding anchor points and connection hardware, employers can enhance the overall safety of their fall protection systems. This better protects their workers from the risks of dropped objects and catastrophic failures.
Workplace Height Safety Compliance Requirements
Ensuring workplace safety at heights is a critical priority for any construction site or hazardous work environment. Adhering to fall protection systems and industry regulations is essential to prevent injuries and fatalities.
Let’s explore the key compliance requirements that employers must observe to maintain a safe work culture.
The legislative’s sets the standard for fall protection systems in the United States. The regulations mandate that employers provide fall protection systems for any work activities conducted at heights of 6 feet or more.
This includes the use of personal fall arrest systems, guardrails, safety nets, and other engineered solutions to mitigate the risk of construction site hazards.
- Legislative requires that all fall protection equipment be properly inspected and maintained to ensure optimal functionality.
- Employers must provide adequate training to workers on the correct use and limitations of fall protection systems.
- Detailed records must be kept of all fall protection equipment, inspections, and training programs.
Beyond legislative regulations, many industries have developed their own safety standards and best practices for working at heights.
For example, the American National Standards Institute (ANSI) publishes guidelines for the design, use, and inspection of personal fall arrest systems. Compliance with these industry-specific standards is often necessary to meet regulatory requirements and ensure the safety of workers.
Maintaining workplace height safety is a multifaceted challenge that requires a comprehensive approach. By understanding the regulatory framework, implementing robust fall protection systems, and fostering a culture of safety, employers can effectively mitigate the risks associated with construction site hazards and protect their most valuable asset – their workforce.
Conclusion
In the world of workplace safety, the need for effective fall protection is clear. This article has highlighted the dangers of falls and the critical equipment and practices workers need to know. It’s essential to understand personal fall arrest systems, the importance of anchor points, and the right connection hardware. A culture of safety is crucial.
Employers and employees can take steps to protect themselves by following the prevention tips and compliance standards discussed. Continuous education and training are key. Staying current with fall protection regulations and industry advancements is vital to safeguard our workforce.
Workplace safety is a collective effort. By working together, we can create a safe environment where everyone can work without fear of falls. Remember, prioritizing workplace safety is not just a legal duty but a moral obligation that benefits us all.